Why We Use 3D Printing (And Why It’s Not the Cheap Option Many Assume)
- Patrick Perry
- Mar 10
- 3 min read
When people hear about 3D printing, they often assume it’s a cheaper alternative to traditional manufacturing methods like injection molding. That’s a common misconception. In reality, 3D printing is often more expensive per part than injection molding, especially when producing large quantities.
At Perry Parts, we don’t use 3D printing to cut costs—we use it because it lets us design and manufacture complex, high-performance parts that wouldn’t be possible with traditional manufacturing.
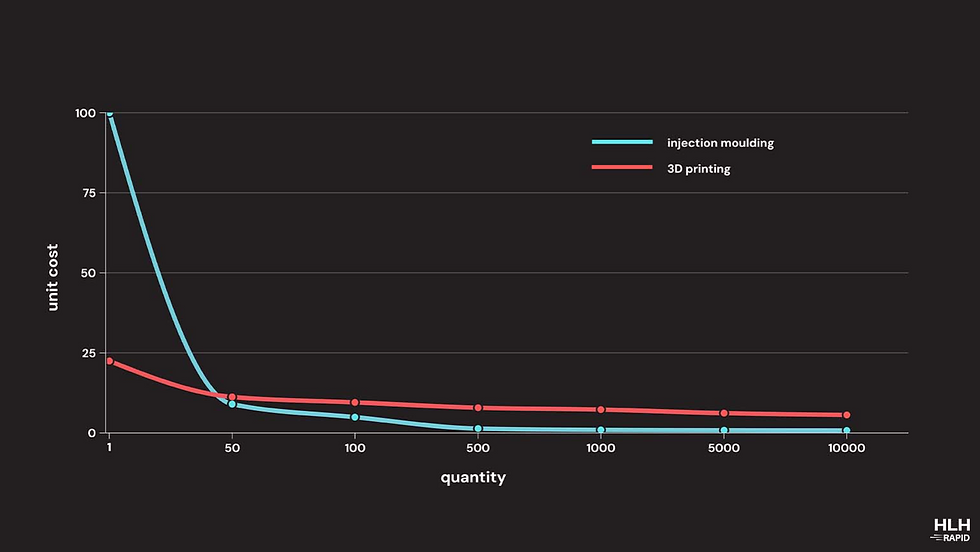
The Cost Misconception: Why 3D Printing Isn’t Cheap
Many people associate 3D printing with affordability because consumer-grade printers have become widespread. But industrial 3D printing for performance parts is a completely different world. Here’s why:
1. Material Costs Are Higher
• Injection molding uses bulk thermoplastic pellets that cost $2 - $10 per kg.
• 3D printing materials (high-performance filaments, powders, or resins) can cost $50 - $500+ per kg.
2. Per-Part Costs Are Higher at Scale
• Injection molding can produce thousands of parts per day, making the cost per unit pennies once the mold is paid for.
• 3D printing is slow, often taking hours per part, and every unit requires the same amount of production time.
3. Labor and Processing Add Up
• Injection-molded parts are nearly ready to use out of the mold.
• 3D-printed parts often require post-processing (support removal, finishing, and inspection), adding time and labor costs.
For mass production, injection molding is almost always the cheaper option—so why do we rely on 3D printing? Because it unlocks design possibilities that injection molding simply can’t match.
Why We Use 3D Printing: It Enables Better Parts
At Perry Parts, our goal isn’t just to make parts—it’s to make the best possible parts. 3D printing allows us to engineer components with advanced internal structures, optimized material distribution, and performance-driven geometries that would be impossible to produce with molds.
1. Optimized Internal Structures
Injection molding requires solid or simple hollow parts. We use 3D printing to create internal geometries that enhance performance.
✅ Variable-density infill: Adjusting stiffness and compliance within a single part
✅ Integrated air channels: Adding compression and rebound damping
✅ Lightweighting: Removing excess material without sacrificing strength
2. Design Without Constraints
Injection molding requires draft angles, uniform wall thickness, and mold-friendly geometries. This limits how complex a part can be.
With 3D printing, we can design:
✅ Tailored shapes for optimal contact angles in the suspension
✅ Non-uniform thicknesses to reinforce critical areas
✅ Integrated hardware retention To make installation faster and easier
3. Rapid Design Iteration & Customization
• Injection molding requires expensive molds that take weeks or months to manufacture.
• 3D printing lets us test, refine, and improve designs in days, accelerating R&D.
• Customization is easy—no need to modify a mold or create new tooling.
The Bottom Line: Cost vs. Capability
Yes, 3D printing is often more expensive per part than injection molding—but we’re not chasing the cheapest option. We’re focused on engineering the best-performing parts possible.
At Perry Parts, 3D printing isn’t a cost-cutting measure—it’s a performance enabler. And when it comes to designing parts that are stronger, more durable, and better optimized for real-world use, that’s a trade-off we’re happy to make.
Want to learn more about how our advanced manufacturing process improves performance? Reach out to us today! 🚀
Sources:
Comments